The production process of an inflatable stand-up paddle (SUP) board involves several stages, including design, material preparation, assembly, and quality control. Here’s a detailed overview of the process:
1. Design and Planning
Concept and Design:
- Design Specification: Define the dimensions, shape, and features of the SUP board based on its intended use (e.g., all-around, touring, racing, yoga).
- CAD Modeling: Use computer-aided design (CAD) software to create detailed 3D models and blueprints of the board.
2. Material Preparation
Drop-Stitch Fabric:
- Core Material: The core of the inflatable SUP board is made from drop-stitch fabric. This consists of thousands of polyester threads that connect the top and bottom layers of the board, allowing it to maintain a flat shape when inflated.
- Fabric Coating: The drop-stitch fabric is coated with a layer of PVC (polyvinyl chloride) to make it airtight and durable.
Reinforcement Materials:
- PVC Layers: Additional layers of PVC are used to reinforce the rails, bottom, and deck of the board for extra strength and durability.
- Traction Pad: A non-slip EVA (ethylene-vinyl acetate) foam pad is added to the deck for grip and comfort.
3. Assembly
Cutting and Shaping:
- Cutting: The drop-stitch fabric and PVC layers are cut according to the design specifications using precision cutting machines.
- Shaping: The cut materials are shaped into the final form of the board.
Welding and Gluing:
- Heat Welding: The layers of PVC are heat-welded or glued together to form an airtight seal. Heat welding is preferred for its durability and cleaner finish.
- Seam Reinforcement: The seams are reinforced with additional layers of PVC to ensure they are strong and leak-proof.
4. Adding Features
Valves and Fittings:
- Inflation Valve: An inflation valve is installed to allow the board to be inflated and deflated easily.
- D-Rings: Metal or plastic D-rings are attached for securing gear or attaching a leash.
- Fin Boxes: Fin boxes are glued or welded onto the bottom of the board to allow for the attachment of removable fins.
Traction Pad:
- EVA Foam Pad: The non-slip EVA foam pad is glued onto the deck of the board. It is cut and shaped to fit the design, providing a comfortable and secure standing area.
5. Quality Control
Inflation and Testing:
- Initial Inflation: The board is inflated to its recommended pressure to check for leaks and ensure it holds air properly.
- Leak Testing: The board is submerged in water or coated with soapy water to detect any air bubbles indicating leaks.
- Pressure Hold: The board is left inflated for a specified period to ensure it maintains its pressure without deflating.
Inspection:
- Visual Inspection: The board is inspected for any visible defects, such as misaligned seams, weak points, or imperfections in the PVC coating.
- Functionality Check: All features, including the inflation valve, D-rings, and fin boxes, are checked for proper functionality.
6. Packaging
Deflation and Folding:
- Deflation: The board is fully deflated and rolled or folded into a compact shape for packaging.
- Accessories: The package typically includes the SUP board, a high-pressure pump, a repair kit, a paddle, a leash, and a carry bag.
Final Packaging:
- Boxing: The board and accessories are placed in a protective box, which is then sealed and labeled for shipment.
7. Shipping and Distribution
Logistics:
- Warehousing: The packaged boards are stored in a warehouse until they are ready to be shipped.
- Distribution: The boards are shipped to retailers or directly to customers via various shipping methods, depending on the destination.
Conclusion
The production process of an inflatable SUP board involves precise engineering, high-quality materials, and stringent quality control measures to ensure a durable and reliable product. Each step, from design to final packaging, is crucial to producing a board that meets performance and safety standards.
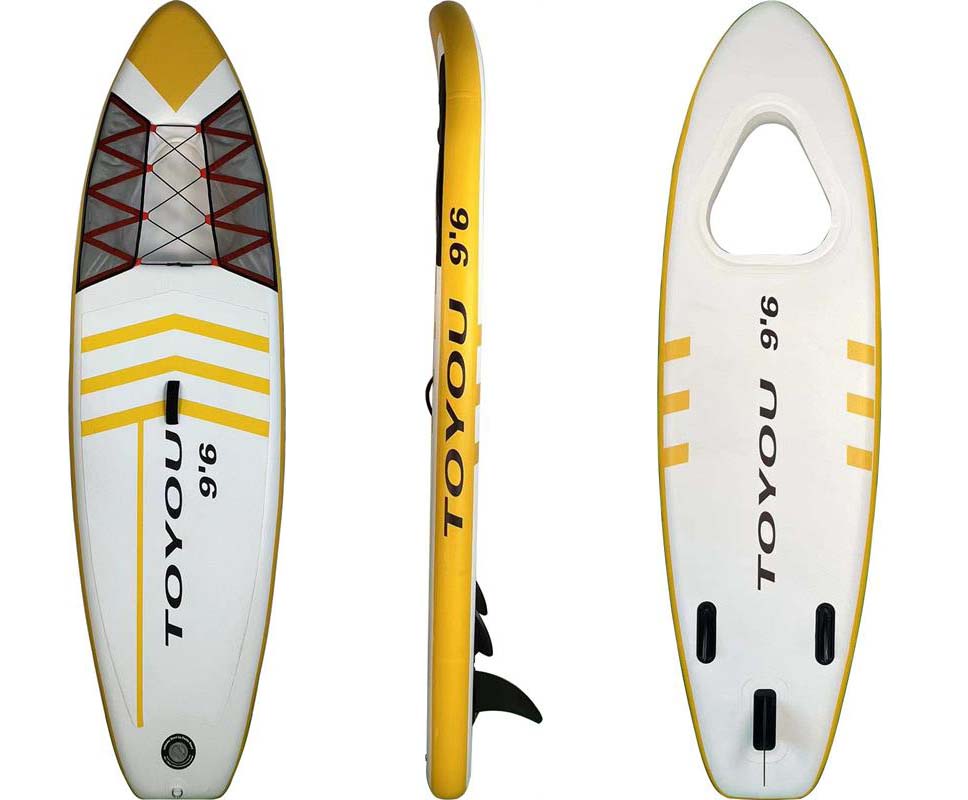
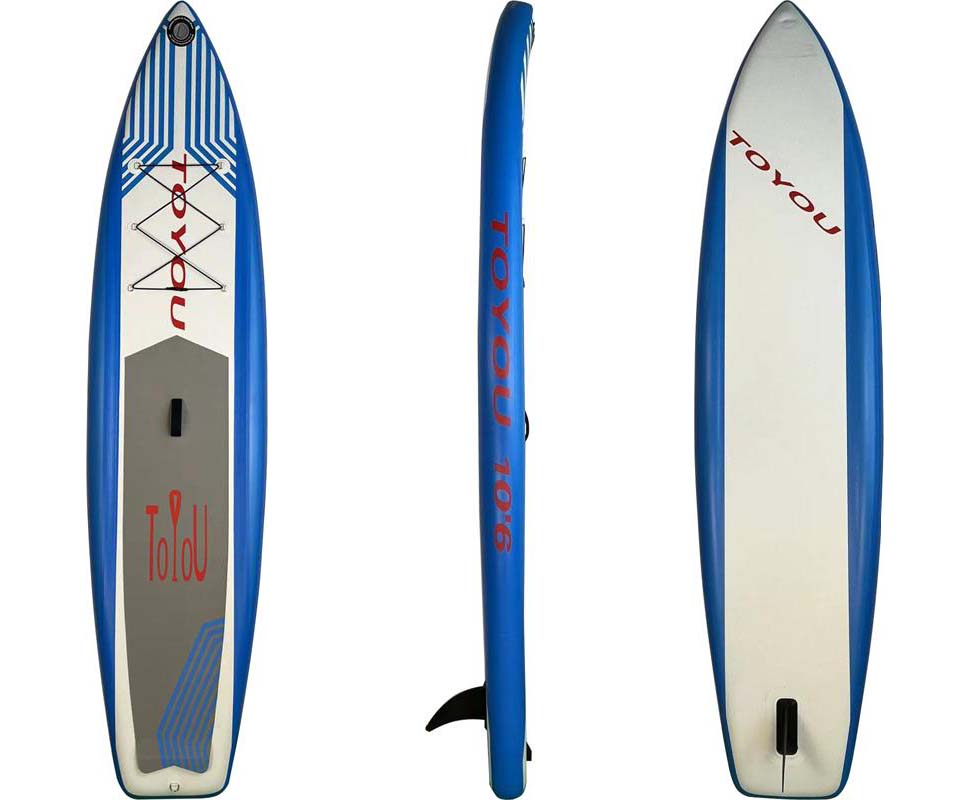